The 17th International Architecture Exhibition proposes not only sustainability through perpetual use, as in the case of European stone construction, but also the sustainability of Japanese wooden architecture, which exists in a variety of forms. This exhibition proposes a sustainable form of Japanese wooden architecture, which is not only sustainable by being used permanently like European stone construction, but also by changing its form in various ways. In the process of this exhibition, I would like to confront old wood again, and think about how to use it in the actual production of furniture. In order to use the old wood with strength, I thought of a way to hybridize it with single pipes, and devised a lathe process using a circular saw. The aged posts and beams, the distortions and scratches on them, all appear as rich expressions.
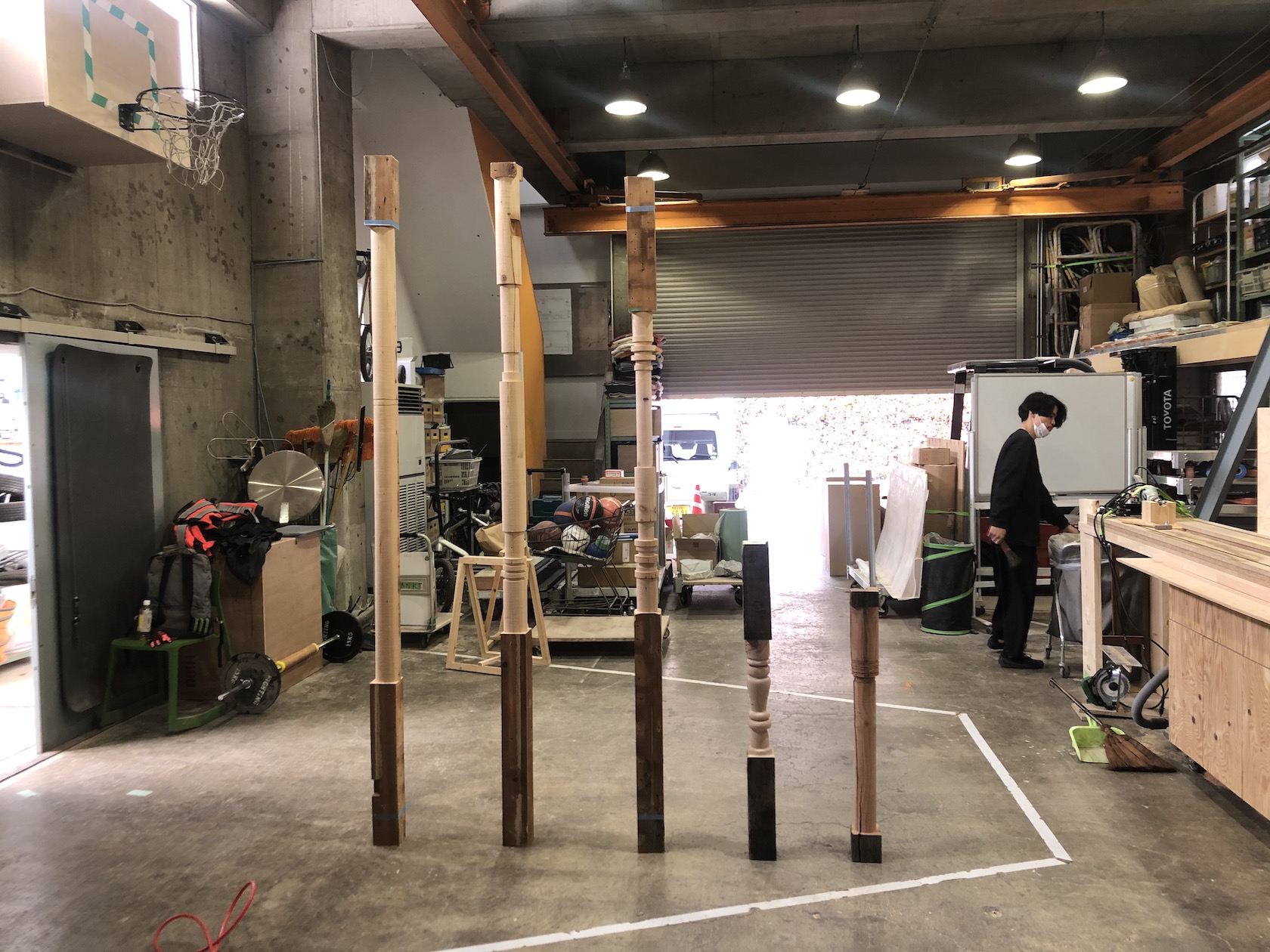
Circular saw lathe
For the past few years, I was a little skeptical about the way the international exhibition took place while participating in Salone del Mobile. Milano or other international Art fair. Even though we live in a day when anyone is able to broadcast at any time what they would like to through Instagram and Facebook and we are able to access information through online architectural and design magazines. However, still many people actually visit the site and such a large amount of the costs and time were spent to make the works domestically and ship them to a distant host country and exhibit them. Of course, it’s important to actually see the works of 1/1 scale with our own eyes, in this day and age I personally think it is more suitable to inquire individually if you find specific works you are interested in and you can visit the place where the works were actually created and have one-on-one conversations with artists or designers.
So when I received the invitation from Mr. Kadowaki, a curator of The Japan Pavilion for VBA, to participate in the Biennale di Venezia, I thought if I participated I would like to make it an exhibition where I could understand the meaning of “moving” as one of the participants. I shared my thoughts and original questions about the international exhibition to the team members and it struck a chord with them so the project started from there. And It became a story to make an exhibit using waste materials that are destroyed and thrown away instead of new materials. At that time it happened that the house in front of Mr. Kadowaki‘s house was demolished, so we decided to exhibit using the waste materials of that house.
While actually dismantling the house, I noticed that the building era also changed and was expanded according to the needs of each era, and the materials of multiple eras overlapped in layers. After this dismantling of the house in Japan, it will be reassembled as an exhibition in Venice and elements will be turned into various exhibits, and after the session is over, it will be moved to Oslo and will be permanently installed again. Our proposal at this exhibition is a sustainable architecture, not only that can be used continuously like the stone architecture in Paris but introducing sustainability such as Japanese wooden architecture, that can be expanded to meet needs, then dismantled, and then re-used while being moved.
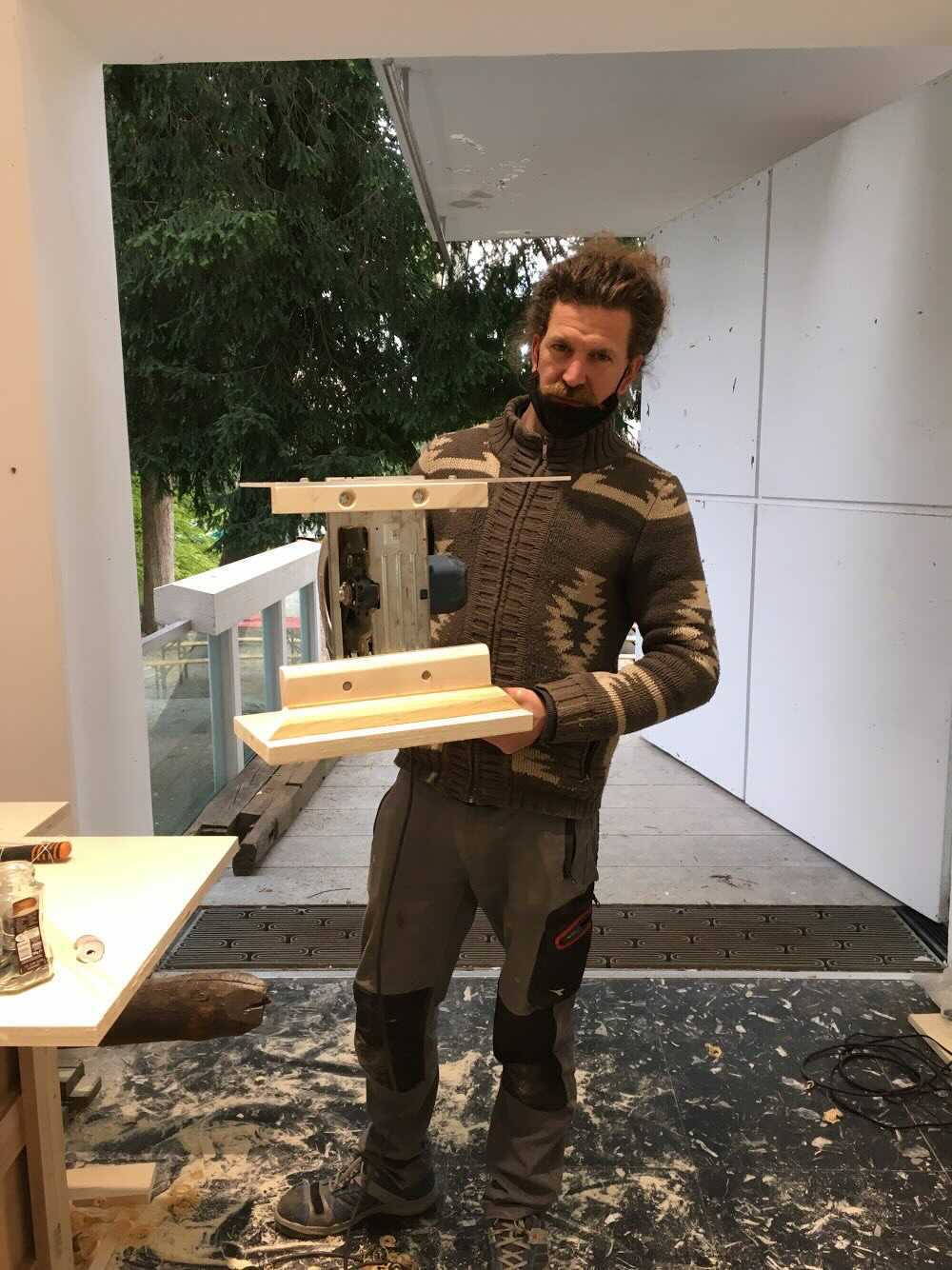
Under such circumstances, since the strength of the old materials themselves cannot be guaranteed sufficiently, we came up with the ideas and it became a common rule for the project to hybridize the single-tube scaffolding to the old materials.
Since originally our roles for VBA were designing the workshop for making the exhibits and the venue, we rarely use old materials, but we use old materials for benches and desks, so I came up with an idea of hybridizing old materials with single tubes and devised this new method of lathe processing with using circular saw.
Through the process, the wood turned into pillars and beams with various dimensions made into a round column, the size of 48.6Φ. Perhaps some people may be wondering why we use circular saws, but it is because the materials have already bent and cracked for over the years, and it is difficult to make a right angle. In addition, the sizes are not even because they are collected from various places. Also even if you put saw to the wood which is processed for the right angle straight away, it will be repelled and lathe processing will not be possible.
Under such challenging conditions, this processing method enables anyone to do the same and produce almost the same quality. And during the process of establishing this method, not only making the materials of the round column of 48.6Φ but also we created decorative connection parts.
With this method of lathe processing with using circular saw, we believe it can be applied not only for old materials but also for making furniture for example with stacking waste plywood. We take this opportunity in Venice and explore more about this method and try to develop a new series of furniture.
7 Comments
calm music
(October 25, 2023 - 4:24 pm)calm music
calm music
peaceful music
(November 18, 2023 - 11:51 am)peaceful music
peaceful music
spa music
(November 21, 2023 - 8:17 am)spa music
spa music
jazz cafe
(December 6, 2023 - 6:02 pm)jazz cafe
jazz cafe
sweet dreams
(December 20, 2023 - 1:50 am)sweet dreams
sweet dreams
relax everyday
(December 21, 2023 - 9:01 pm)relax everyday
relax everyday
fireplace sounds
(December 26, 2023 - 9:23 pm)fireplace sounds
fireplace sounds
Comments are closed.